
Orbital welding


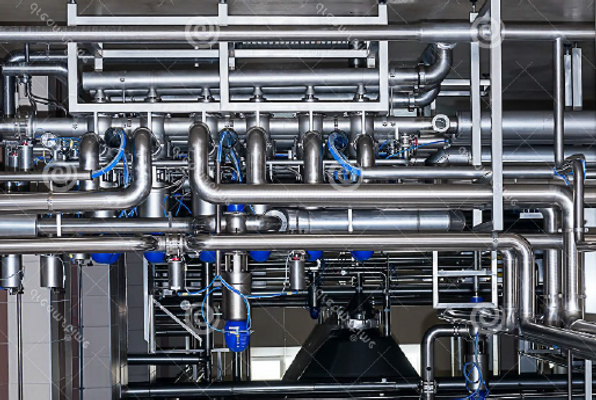
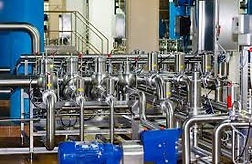
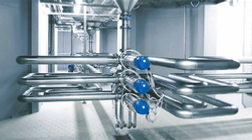
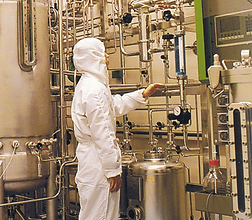
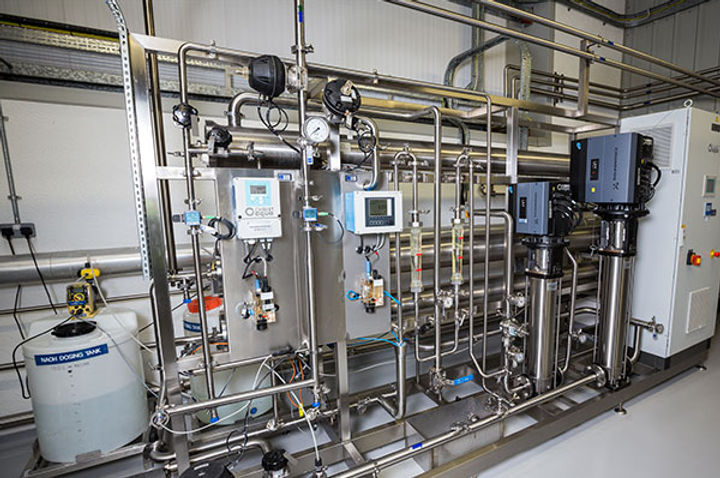
Gas control technologies use orbital welding to ensure the highest standards of quality and safety. Orbital welding is a standardised and computer controlled process that produces consistent high purity results. High purity means that there is no oxidisation/contamination after the weld process present on the inside wetted surface of the tube that carries the process gas.
Because of the inherent control of the orbital welding process, the smallest standard tube diameters from 1/8” can be processed. On a larger scale, pipes with diameters up to 170mm and walls up to 3.5mm thick can be joined by orbital welding. Gas control technologies are currently developing an orbital welding process for pipe up to 6mm wall thickness.
Pipe systems joined by orbital welding ensure maximum safety and purity levels for delivering process gases. The orbital weld quality will effect the gas purity delivered to the tool. Internally, orbital welds should be smooth in appearance and not discoloured. Discolouration represents oxidisation from the orbital weld process and this oxidisation introduces impurities into the process gas and consequently can effect the results.
Orbital welding can be used for many different material types, including high-strength, high-temperature and corrosion-resistant steels such as (316L EP SS) which is typically used in clean room applications associated with the semiconductor industry and thin film coating processes such as MOCVD.
Orbital welding is also utilised in other industries requiring welded stainless steel pipe work such as food processing, beverages, pharmaceuticals, chemical engineering, and biotechnology. Orbital welding offers the advantage of integrity of process gas delivery and increased safety over compression fittings and is cost effective.
Size
-
1/8” (3mm) to 4” (100 mm)
Materials
-
Stainless Steel - 316L & 304
-
Nickel Alloys
Specifications
-
Welder – BS EN 1418 – 1998
-
Weld – CFS Specification
Plant
-
Welding Set – ARC Machines 207
-
Weld Head – ARC Machines 9500
Purged with Argon